SunSPEC 4
Singapore Polytechnic
Solar Team
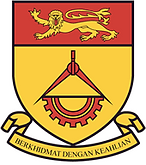
Week 1 (20 April - 24 April)
|| For the first week, we went through the World Solar Challenge 2015 Regulations before we start implementing the solar car. The link below is about the regulations.
http://www.worldsolarchallenge.org/files/522_2015_world_solar_challenge_event_regulations.pdf
Following regulations are the most important to our solar car team.
- Cruiser Class scoring has been adjusted, and charging from the grid will be allowed only in Alice Springs.
- Electrical isolation requirements have been changed to make it easier to supply low voltage to the Solar EV when the high voltage system is isolated, and at the same time define a ‘safe state’ as the vehicle system default.
- A requirement to make provision for a data logging device has been introduced.
- Challenger Class and Cruiser Class Solar EVs must be no more than 4500 mm in length, no more than 1800 mm in width and no more than 2200 mm in height (above the ground) at any time while charging or driving . (Box Dimensions of Car)
- Solar EVs must be constructed or adapted to protect, as far as is reasonably possible, the occupants in the event of collision or roll-over. Steps should be taken to ensure that the structure (such as the solar collector), components or accessories will not impinge on the occupant space in a crash.
- Any cruise control function must automatically deactivate when the brake or accelerator pedal is operated, and when the main switch is turned off.
- All high-voltage parts must be protected by covers or protection grills that are reliably secured and marked with the approved high voltage symbol.
- All wires, connectors and electronics modules (such as MPPTs) which remain at high voltage when in Safe State must be double insulated.
- Double insulated components must meet the AS3001/IEEE 100 (UNECE100) definition of double insulation as comprising both basic insulation and supplementary insulation. A single layer of reinforced insulation is also acceptable. The surfaces of a photovoltaic cell are deemed to be double insulated if properly encapsulated. Unencapsulated surfaces of pv cells, interconnects and associated wiring must be double insulated.
- The Solar EV must have a Safe State which minimises the risk of electrical fire and electric shock to occupants, team members, emergency response personnel or bystanders.
- When in the Safe State:
- All conductors emerging from the energy storage packs must be galvanically isolated from
the energy storage devices inside those packs.
- No conductors emerging from the energy storage packs or solar collector may carry high voltage, even though galvanically isolated.
- All conductors emerging from the solar array must be isolated from all circuitry in the rest of the car by one or more a mechanical switches or contactors.
- Devices used to concentrate solar irradiance may be used, provided that they are a permanent part of the Solar EV and the configuration of the car does not exceed the dimensions specified in Regulation 2.2.1
- For Challenger Class and Cruiser Class Solar EVs, if the solar collector uses photovoltaic cells then the allowable area of photovoltaic cells is:
- not more than 6.000 square metres for Solar EVs using only silicon photovoltaic cells
- not more than 3.000 square metres for Solar EVs using only GaAs photovoltaic cells.
- Challenger Class and Cruiser Class Teams wishing to use other types of photovoltaic cells, a mix of photovoltaic cell types, or other types of solar collector, must contact the Organiser.
- Each Solar EV will be required to carry a data logging and tracking device provided by the Organiser. Provision must be made for a box, maximum dimensions l= 200mm x w=150mm x h=100mm, to be fitted in the Solar EV. The upper face of the box will require a minimum 1.6Ï€ steradian view of the sky through a minimum 125mm diameter circular window made of a radio-transparent material. The mass of the unit will not exceed 5Kg.
|| We had a discussion with Mr. Than on 24.April.2015. From this meeting, we decided to print 3D model of solar car, SunSPEC4. It is for easy visualisation as a reference when we have a discussion among ourselves or with other team members.
We got the 3D design file from Mr. Foo from Mechanical Engieering. The design is shown in Fig. 1.
Fig. 1(a) Front part of solar car body Fig. 1(b) Rear part of solar car body
Fig. 1(c) Front part of solar panel Fig. 1(d) Rear part of solar panel
The car body is splitted to two parts. It is because we want to print bigger size of model. We brought these design to fab lab to print them out. Each design took around 6 to 9 hours to print.
|| From the discussion, we also confirmed the size of the margin and string D. The margin size is 10mm as if the margin size is small, it can cause the damage of the solar panels. The size of string D is (1158x383)mm² without margin. With margin is (1180x400)mm².
Week 2 (27 April - 1 May)
|| We printed 3D model of solar car body and panels. The bictures of 3D model are shown below.
Fig. 2(a) Front side of solar car Fig. 2(b) Rear side of solar car
Fig. 2(c) Overview of solar car Fig. 2(d) Overview of solar car
Fig. 2(e) Solar panels
However, we failed to print perfect 3D model of the solar car body. When we cut the support inside the car body, the wall of the solar car was also tore together with the support. It is because the wall of solar car is very thin so the solar car is very flimsy. Therefore, we could not get the perfect 3D solar car model.
To solve this problem, we came out with one solution which we use thicker and stronger wax for printing 3D model, so that we could have a strong wall for solar car model.
|| We studied the SunSPEC 3 and SunSPEC 4 and we compare both cars.
SunSPEC 3
- Challenger Class (Driver)
- Solar Cell
- C60 Cell from SUNPOWER
- Cells with rough surface
- Bypass diode due to shadowing by canopy
- MPPT
- Boost-up Micro MPPR from Nomura
|| From tge discussion, we considered to install the energy meter into the solar car. We did some research on it to confirm whether to use the energy meter. Energy meter is a kind of monitoring system but it is slightly different from the telementry system.



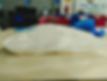


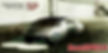

SunSPEC 4
- Cruiser Class (Driver with an assistant)
- Solar Cell
- E60 Cell from SUNPOWER
- Cells with laminated surface
- NO Bypass diode as there is no canopy
- MPPT
- MPPT-Race V4.0 from Drivetek
Week 3 (4 May - 8 May)
|| We studied the total power for the solar cells (String A,B and C) with the sun elevation and azimuth angles for different times of the day at Darwin.
Driving: 5.141 kWh
Sunning: 1.357 kWh
Total: 6.498 kWh
|| This is an another attempt for printing 3D model of solar car, but we failed again.
Fig. 3(a) Front side of solar car Fig. 3(b) Rear side of solar car
Fig. 3(c) Overview of solar car Fig. 3(d) Overview of solar car
As you can see from Fig. 3, the wall of the soar car are still very thin so it is easily broken. We need to find the way to improve this problem. For 3D model of solar panels, we decided not to print it as 3D model as it does not fit to 3D car body and the panels are not flexible so it is difficult to mount on the car body. Therefore, we use thick paper instead as it is flexible so that it can fit onto the 3D model of car body.
|| We decided to design and install the energy meter. It will be beneficial to use the energy meter as it shows the value of voltage, current and power between the solar panels and MPPTs. By installing the energy meter, we can check whether there are some problem like loosen wires between panels and MPPTs.
We are using Arduino UNO because we have to use same Arduino set as the telementry group.
|| We visited the factory to see the actual solar car. We measured the actual size of the solar car to check whether the solar cells can fit into the solar car. The pictures below are showing the actual body of the solar car body.
Fig, 4(a) Inside of the solar car Fig. 4(b) Inside of the solar car
Fig. 4(c) Placement of Sting B and C Fig. 4(d) Overview of solar car
Fig, 4(d) Front view of solar car
We used the tailor tape to measure the car body as the tape is flexible and can measure curve parts of the solar car. When we measured the actual size of solar car, we have limited space for the solar cells to mount on the solar car. As the mechanical side requries additional space, 10mm to cut the carbon fibre where the solar strings are placed.
The diagram below is actual solar car body size. (See Fig. 5)










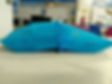











Fig. 5 Actual body size of solar car
Week 4 (11 May - 15 May)
|| Comparisom between the calculated value of String A,B and C and actual body size. This is to check whether the solar strings have enough space to fit onto the car.
The diagram below is the String A, B and C with calculated value. (See Fig. 6)


Fig. 6 String A, B and C with calculated value
As you can see from Fig. 5 and 6, the difference in length between the actual solar car body and the strings are very small. Some parts of actual body size is longer than the estimated value of solar car. Also, we have to give extra 10mm to Mechanical side for cutting the carbon fibre. Therefore, we have problem as there is a limited space for the strings to mount on the solar car. Especially, String C seems that it has a serious problem compared to other strings as it has most limited space.
To solve this problem, we measured the actual solar cell size to make sure we have enough space for the solar cells to fit onto the solar car body.
The diagram below is the actual solar cell size. (Fig. 7)


Fig. 7 Actual solar cell size
When we compare Fig 5, 6 and 7, we discovered that we have enough space for the solar strings to mount on the solar car body. It is because the actual solar cell size is shorter than the estimated value. Therefore, there is no problem with solar strings to fit onto the solar car.
|| From the discussion, we consider to use either copper tape and AWG 14 wire for connection between solar panels and MPPTs.
Specification of AWG 14:

Specification of Copper tape:

We should calculate the resistance for each material. Higher resistance will cause higer power loss. Therefore, we will consider to choose the material with less power loss.
The equation below is for calculating the resistance.
(Copper Tape) (AWG 14)

Week 5 (18 May - 22 May)
|| We are not using bypass diode for SunSPEC 4. For SunSPEC 3 has a bypass diode as it has a canopy which causes the shadowed cells but SunSPEC 4 does not have a canopy. (See Fig. 8 and 9) There will be less possibility to have a shadowed cells unless there are tress or clouds. However, the trees rarely exist in Australia as the competition is held at desert. Also. the clouds are hard to be seen at the racing place because of the wheather condition in Australia. These factors will not damage much the cells by shadowing as these are not making shadow for long term. Only long term shadowing will cause the hotspot on the cells and damage the cells. Therefore, we decided not to use the bypass diode.


Fig. 8 SunSpec 3 Canopy Fig. 9 SunSPEC 4
|| We made a negative view of the solar panels. (See Fig. 10) As all the current images are top view of the solar panels. These images will be helpful when we doing the wiring as we are doing works under the carbon fibre. Since we seeing the view from below part of the solar panels, we are easy to imagine the placement of the hole.


Fig. 10 Negative view of the solar panels
|| We visited the factory again to check whether we have enough space for the solar panels to mount on the carbon fibre. We cut the paper as same size as the cell size.



Fig. 11 Paper cut-out for String A Fig. 12 Paper cut-out for String B
The image below shows how we put the paper on the carbon fibre and check wheter have enough space. (See Fig.13)
Fig. 13 Paper cut-out for String C
|| We designed the wiring of both AWG 14 and copper tape for String A, B and C. We designed two possible wiring for AWG 14 wire. If we are using the AWG 14 wire for connection, we choose the design with lower resistance and easier implementation process.

Fig. 14 First Trial for AWG 14 Connection (String A&B)

Fig. 15 First Trial for AWG 14 Connection (String C)

Fig. 16 First Trial for AWG 14 Connection (String D1&D2)
The diagrams below are showing the second trial for AWG 14 wire connection design.

Fig. 17 Second Trial for AWG 14 Connection (String A&B)

Fig. 18 Second Trial for AWG 14 Connection (String C, D1 & D2)

Fig. 19 Copper Tape Connection (String A&B)
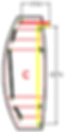
Fig. 20 Copper Tape Connection (String C)

Fig. 21 Copper Tape Connection (String D1 & D2)
Week 6 (25 May - 29 May)
|| We calculate the total resistance for each desgin of AWG 14 and copper tape. With the resistance values, we can compare the power losss of AWG 14 and copper tape. Therefore, we can choose the material for the connection between solar panels and MPPTs.
Calculation of the total resistance of first trial for AWG 14 Connection:
Stirng A&B:

String C:

String D1:


String D2:
Total Resistance: 39.2mΩ
Total Power loss: 0.63Wh
Calculation of the total resistance of second trial for AWG 14 Connection:
String A&B:

String C:

String D2:
String D1:


Total resistance: 33mΩ
Total power loss: 0.53Wh
Calculation of the total resistance of copper tape connection with 20mm of width (Single Layer)
String A&B:

String C:

String D1:

String D2:

Total resistance: 120.4mΩ
Total Power loss: 1.93W
Calculation of the total resistance of copper tape connection with 20mm of width (Double Layer)
String A&B:

String C:

String D1:

String D2:

Total Resistance: 60.2mΩ
Total Power loss: 0.96Wh
Calculation of the total resistance of copper tape connection with 30mm of width (Double Layer)
String A&B:

String C:

String D1:

String D2:

Total resistance: 40.2mΩ
Total power loss: 0.64Wh
Calculation of the total resistance of copper tape connection with 50mm of width (Double Layer)
String A&B:

String C:

String D1:

String D1:

Total Resistance: 24.2mΩ
Total power loss: 0.39Wh
Therefore, we decided to use copper tape with the width of 30mm even though 50mm has lower power loss. Since the insulation tape's width is 50mm which is safer to use 30mm as we can perfetly cover the copper tape with the insulation tape in layers.
|| We decided to use copper tape with the width of 10mm and insulation tape to connect the solar strings to solar strings. The diagram below shows how we will connect them using the copper tape and insulation tape.

Fig. 22 Wiring connection between solar strings
|| For 3D model of solar, we kept failing to print it, because of its thin and weak walls of the solar car. However, we found one program that is called "Meshmixer", it increases the thickness of the wall and makes a support at the weaker parts. The diagrams below show how Meshmixer increase the thickness and make support. (See Fig. 23)


Fig. 23(a) Front Part of 3D model Fig. 23(b) Rear part of 3D model
With these design, we printed 3d model of solar car succesfully. The pictures below show succeed 3D model of solar car. (See Fig. 24)


Fig. 24(a) Front Part of 3D model Fig. 24(b) Rear Part of 3D model
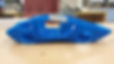

Fig. 24(c) Overview of 3D model Fig. 24(d) Overview of 3D model
We also cut the paper as the string size. The pictures below show the paper strings on the 3D model of solar car.
(See Fig. 25)


Fig. 25(a) Paper cut-out for string A&B Fig. 25(b) Paper cut-out for string C